The Tech Inside AC75 Soft Wings
by Ivor Wilkins 2 Apr 2021 00:00 NZDT
2 April 2021
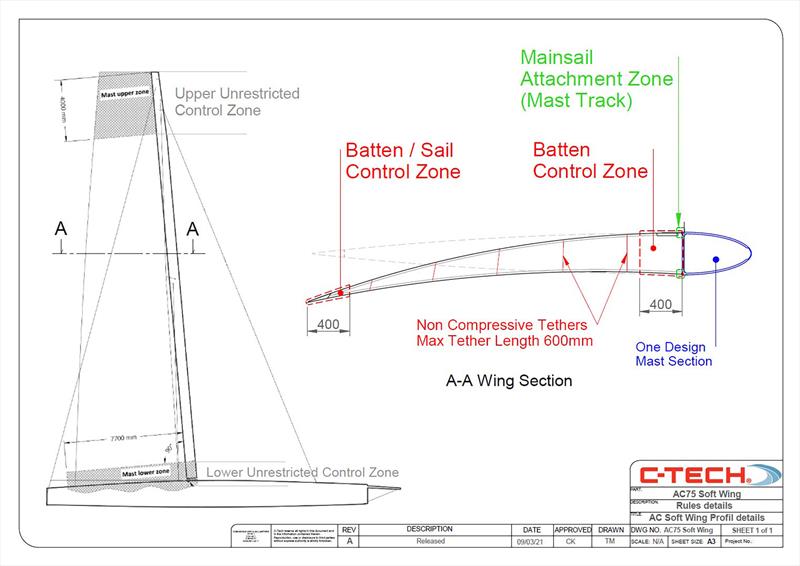
AC75 soft wing control zones © C-Tech
In their pursuit of astonishing speed, the foiling AC75 monohulls of the 36th America’s Cup represent the highest level of precision engineering across thousands of components – most of which are hidden from view. Auckland composite engineering company C-Tech has provided a host of custom carbon elements for the four teams competing in the current Cup regatta.
“We have supplied a wide range of items, including specialist struts incorporating titanium fittings, some related to the internal hull structures, some for aerodynamic fairings, along with items like mast tracks and grinding pedestals,” says director Alex Vallings. “Some of the items are top secret and even we don’t know what they are for.”
All require precise lightweight engineering to the finest tolerances. In a high-stakes racing environment, every item must provide strength and reliability under enormous loads at the lowest possible weight.
C-Tech’s biggest involvement has been in the design and manufacture of sail battens, with all four teams using their products. In simplest terms, battens are horizontal ribs running across the surface of the sail, acting as a skeleton to provide structural support and shape.
At America’s Cup level, they are highly engineered, complex pieces of equipment tailored to perform very specific functions under closely defined conditions.
At a glance, they look like nothing more exciting than long black extrusions with hollow box-shaped sections of approximately 40mm X 20mm. In reality, they are vital, high-tech pieces of equipment – performance-enhancing magic wands.
“Battens play a key role in the performance of the sails,” says North Sails’ Gautier Sergent who worked on the British INEOS campaign. “It is very important to ensure they match the expected shape of the sail in the way we specify. If the shape of the batten does not exactly match the shape of the sail, they fight each other and that can be quite detrimental.
“They must be light and strong. We specify the stiffness we require and the distribution of stiffness on each batten and C-Tech are able to match that very accurately and repeatedly.”
“Essentially, you can think of each batten as a small carbon mast,” says Alistair Campbell who specialises in this area. “These battens represent levels of technology in terms of loading and manufacturing techniques similar to the carbon masts you see on sports boats like 49ers or Moths.”
There are between nine and 12 battens, varying in length from 3m to 7.3m, for each membrane. Depending on wind strengths, each mainsail has different configurations, requiring batten sets with different stiffness characteristics. Across a typical three-mainsail inventory, that would represent more than 100 pairs of battens, each pair individually designed and engineered to precise specifications. The AC75 headsails also carry between five and eight battens each.
With these yachts reaching speeds of over 50 knots, their sailplans are exposed to the equivalent of storm-force apparent wind speeds of 60-70 knots, demanding a high level of durability and aerodynamic efficiency.
And, like every other component on an America’s Cup or other grand prix yacht, they must perform against contradictory criteria: highest durability at lowest possible weight.
“With an entirely new class, the teams have been learning a lot about what makes these boats go fast, so the parameters are changing all the time. We are dealing with moving targets,” says Vallings. “For example, early on a team might say the mainsail camber will not exceed 13-15 percent. Then, we discover they are actually sailing with camber nearly double that at times – well outside the original design limit.”
That process of pushing boundaries began right back when the AC75 rule was being written. “There was a lot of pressure to get weight out of the sail plan. They came to us and asked what the weight of the battens were going to be,” Vallings recalls.
At that stage, the stiffness and shape characteristics were unknown, so an estimation had to be made at 22kg for a set of mainsail battens. C-Tech manufactured a prototype set and it came out at 26kg. “Panic stations,” Vallings laughs. “We had to start again and shed weight.” Working closely with the teams, C-Tech found ways to reduce weight, despite being challenged to add durability and stiffness along with hardware/sail integration components.
After much head-scratching, design iterations and testing, most batten sets came out at between 24-29kg, including the additional hardware. Some of the battens had to muscle up to provide some of the structure typically provided by a boom.
The twin membranes of the mainsail are hoisted on separate tracks 400mm apart on the flat aft surface of the D-shape mast section. The two leeches are held together on a fixed-length tether. The concept is to create a foil shape similar to an aircraft wing.
Within tight area constraints, designers have two free-zones – in the bottom 1.5m and the top 4m – where they can utilise hydraulic internal control systems to manipulate the wing shape to best performance advantage. With the mast able to rotate up to 45° each way, the whole structure is highly dynamic, capable of inducing considerable degrees of twist and camber up and down the length of the sail.
Where the batten ends attach to the mast is another 400mm diameter free zone, within which designers can introduce control systems. “It goes to the next level when you can control the depth of the sail and the angle to the mast with a control system,” says Alistair Campbell. “All the teams have had different thoughts on this. Some have tried hard to constrain the movement of battens, others have taken a passive approach and allowed the battens and sails to do what they want, and some have introduced active control systems.
“What we can say is that in some situations the battens experience a 40° angle change between the mast attachment area and the leech. We never anticipated that and neither did the teams.”
According to Rob Salthouse from Emirates Team New Zealand, C-Tech has been closely involved in their sail programme throughout the current America’s Cup cycle. “With the introduction of the twin-skin mainsails and the speed of the AC75s, the battens play a big part in sail shape and reliability for our programme.”
The design and engineering challenge for C-Tech is to tailor each pair of battens to provide the exact degree of curvature along their length to match the desired shape of the sail and respond precisely to the considerable loads involved.
This involves another contradiction: the area closest to the mast carries the greatest bending load. Yet that is where the batten is required to provide the greatest flexibility to match the curvature of the sail, which is most acute at the mast end and flattens out towards the leech.
Further complicating the equation, the leeward sail membrane has considerably more camber than the windward membrane, placing different demands on the battens as they swap from one tack to the other.
To overcome these conflicting challenges is where the C-Tech team apply their engineering and manufacturing magic. Like the AC75s themselves, the solutions are concealed on the inside. Although the external profile of each batten looks uniform along its length, the dimensions of the interior surfaces vary considerably, depending on the load and flex specifications.
“Every batten is individually designed for its specific position on the sail and every metre of that batten is specifically engineered to provide the degree of camber it needs to match the optimum sail shape at that point, with the strength to accommodate the loads,” says C-Tech’s Chris Kitchen.
“To begin with, the teams were miles apart in their exploration of the rule. As their knowledge and experience has grown, they are much more precise about what they want and a lot more defined about where they want the stiffness to be.”
Utilising C-Tech’s custom in-house design software, it takes up to two weeks to design and manufacture a set of AC75 mainsail battens. As the process has progressed, attention has turned to the detailing of the batten ends both at the mast and leech.
To improve aerodynamics at the leech-end, a post-production tapered section has been added to bring the section down to 40mm x 3mm, while the most common mast-end system involves a simple snug-fitting rectangular box section receptacle. The batten slots inside the receptacle, which the teams connect to their particular control systems.
Working with the teams on individual components and sail hardware has been another area of C-Tech’s contribution. “Their flexibility in design and build, combined with a willingness to collaborate on ideas, helped in producing the best components for our needs, giving us the best results,” says ETNZ’s Rob Salthouse.
The America’s Cup is about the most secretive and competitive environment of any sailing contest. Working across all four teams and guarding their respective secrets has been at the forefront of C-Tech’s agenda. Strict non-disclosure agreements provide a strong legal imperative to avoid intellectual property leakage, but an even stronger consideration is the company’s reputation for integrity. “We have built up a level of trust over 20 years and we place enormous value on that,” says Vallings. “It is a foundation the business has been built on and we have had the privilege of working with the best racing syndicates over the years.”
To learn more about C-Tech click here.