10 days left to win back up to (NZD)$1,000 of your Antifoul cost with Altex Coatings
by Abbie Clark 21 Jan 2022 16:59 NZDT
21 January 2022
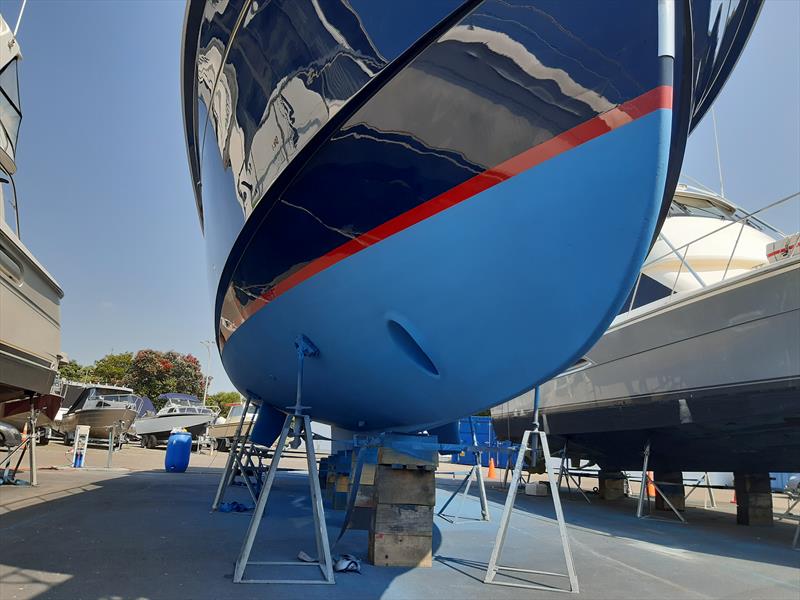
Altex Hydrocoat antifoul © Altex
The opportunity to win back up to (NZD)$1,000 of the cost of your Altex Coatings Boat Paint or Pettit Vivid or Pettit Hydrocoat branded Antifouling finishes on 31st January. However, there is still time to send your proof of purchase to be in the draw.
Simply send either a copy or image of your proof of purchase, invoice or receipt, to Altex Coatings competition email or Facebook messenger and you're in to win the cost of your antifoul loaded onto a pre-paid card! The Altex antifoul paints included in the promotion include No.5; No.5 Plus; Seazone 60; Pettit Antifouling Paint and Hydrocoat.
To see more details visit altexboatpaint.com
Altex Coatings Ltd specialises in the formulation, manufacture, and specification of high performance marine protective coatings throughout Australasia and the South Pacific. Professional and knowledgeable service, enduring customer relationships, providing world-class products backed by world-class technology for hard wearing marine environments we have the coating system for your asset
Here's some helpful tips from the technical team at Altex Coatings, on how to get the best results from their fine products.
For new anti-fouling to adhere to old anti-fouling - and work - there is one major prerequisite: Compatibility.
To be compatible for recoating, the surface must be known to meet the following criteria:
- 1. Be Clean - free of all slime, shell, and other foreign matter (including sanding dust, if applicable).
- 2. Be Sound - no cracking, spalling, laminating or “over-thickness” areas.
- 3. Be Chemically Compatible - there should be no adverse reaction between new and old coatings, either at the time of application or whilst in service.
Items 1 and 2 above are within the control of the boat owner/applicator/contractor. Item 3 – please consult with the FREE AY&B Technical Services Dept or via our website if you cannot determine what has previously been used, then it is advisable to either full seal it off with PrimaShield Antifouling Sealer or fully remove.
Be Clean: Excellent results will be achieved by employing one of the two cleaning processes below:
- Either: waterblast immediately after slipping with 5,000 psi to remove ALL growth, slime and hydrolysed (spent) antifouling
- Or: waterblast immediately after slipping with 2 -3,000 psi to remove MOST growth, slime and hydrolysed (spent) antifouling AND then thoroughly wet sand all surfaces with 80 grit, and plenty of fresh water to remove the last residues of slime, salts, shell growth and hydrolysed antifouling.
The surface, once dry, will be free of any antifouling dust – wipe the surface with your hand, if your hand comes away clean, then the surface is generally well prepared.
Be Sound: A sound surface is one free of cracks, lumps, spalls etc. that requires no further preparation before recoating. Beware of excess season to season build-up of anti-fouling as this can lead to cracking and spalling, even though the surface appears sound. As a rule-of-thumb, it is advisable to strip back every three or four slippings to prevent build-up of old coatings.
Cracking often does not show up for several days after slipping, even though it can occur within hours. Cracking is induced by several factors such as excessive thickness of the total installed anti-fouling, excessive thickness of any one application, less than perfect adhesion of the anti-fouling system to the substrate and/or contamination between coats of anti-fouling.
This tendency to crack is a dynamic situation which once started will continue to its final undesirable conclusion. Such dynamic failures often show up as a total cracking and spalling of the entire anti-fouling the first slipping after a previous “perfect” slipping, cleaning and recoat. Hence the need for attention to detail and the recommendation to strip the anti-fouling system from time to time to prevent build-up.
Be Compatible: Altex No.5 and Sea~Zone 60 Antifouling may be applied over most properly prepared antifouling’s, but with notable exceptions. All acrylic tin copolymer antifouling’s should ideally be stripped, however it is possible to prevent tin-leaching and stabilise the surface for re-coating by applying two roller coats of AY&B PrimaShield Antifouling Sealer. “Singapore” and soluble matrix types will need to be thoroughly sanded to remove spent matrix skeleton and may also require sealing with AY&B PrimaShield Antifouling Sealer.
Pettit Vivid Antifouling can be applied over most properly prepared aluminium safe antifouling’s using the surface preparation outlined above.
Sea~Zone 60 may be applied over most properly prepared cuprous oxide based antifouling’s using the surface preparation outlined above, however, we recommend that greater attention to detail be employed to ensure a very stable substrate prior to overcoating.
When in doubt, strip the existing anti-fouling back to the bare hull or sound primer barrier system and treat as for new work.
A variety of cleaners and primers are available from your Altex Yacht & Boat Paint Distributor, as well as the AY&B Antifouling brochure which lists the products available, the coating system to use.
Please note that No.5 / HydroCoat / Sea~Zone 60 Antifouling’s are not suitable for use on aluminium alloy surfaces. Please refer to Vivid Aluminium Safe Antifouling.
We recommend to refer to individual datasheets (available on our web site) for specific application, as no two antifouling are the same. Our Technical team can assist your product selection and let you know your closest reseller. Available from all leading chandleries, marinas and retailers across Australia.
Don’t forget to check out the summer promo! altexboatpaint.com